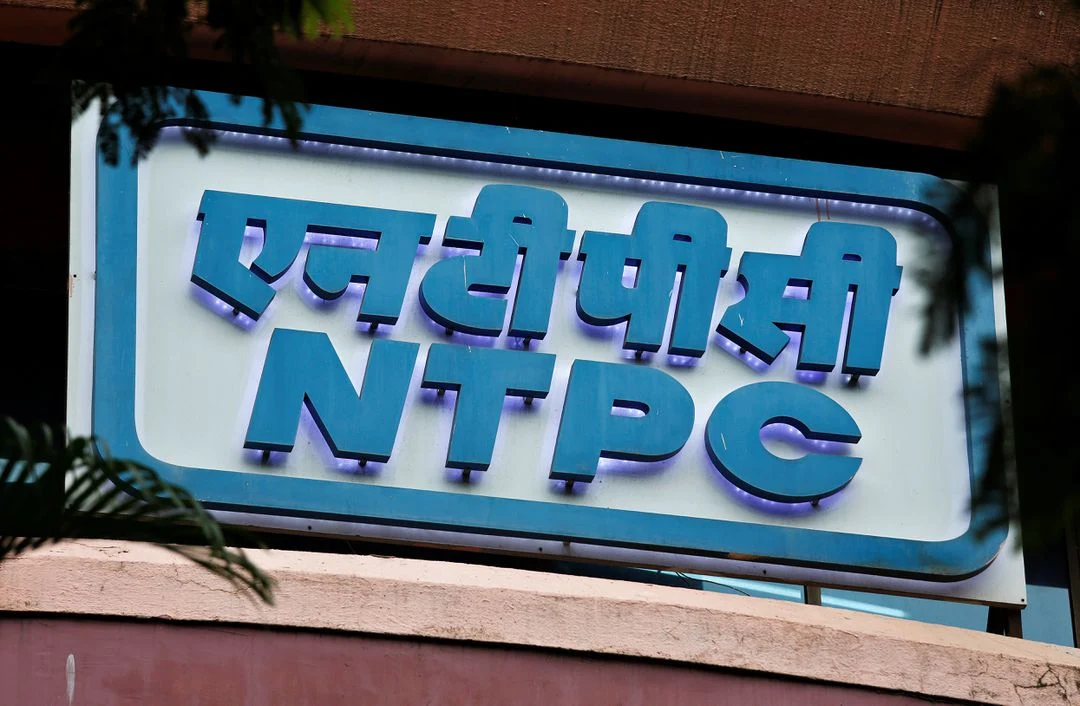
Carbon capture is underway at NTPC’s 500MW coal-fired power plant (Unit-13) at Vindhyachal Super Thermal Power Station, in Madhya Pradesh, India.
NTPC Energy Technology Research Alliance (NETRA) has selected Carbon Clean and Green Power International Pvt. Ltd to set up the carbon capture plant at NTPC Vindhyachal. This plant is designed to capture 20 tonnes of carbon dioxide (CO2) per day, which will use a modified tertiary amine to capture CO2 from the flue gas of the power plant. The CO2 will eventually be combined with hydrogen to produce 10 tonnes per day of methanol through a catalytic hydrogenation process.
The capture of CO2 from the flue gas of coal-fired power plants, and its conversion to methanol, is a priority area for NTPC and is expected to create potential new business opportunities and revenue streams for the company.
Aniruddha Sharma, Chair and CEO of Carbon Clean, said, “We are thrilled to see our technology begin to capture carbon from NTPC’s plant and look forward to seeing how the CO2 to methanol project develops in the future. This project demonstrates how carbon capture supports industrial decarbonisation, as well as providing opportunities for companies to join the growing circular carbon economy.”,
Surbhi Puri, Director, Green Power International added, “It is a great honour and achievement to successfully demonstrate the carbon capture project at NTPC’s Vindhyachal plant. It is a matter of great pride for us to work with Carbon Clean on this project that will help deliver a greener and cleaner future. Decarbonisation through carbon capture is the future. With this small contribution towards the net zero economy, we hope to inspire the industry to make further strides in this decarbonisation drive.”
Carbon Clean’s CDRMax™ carbon capture technology can be used with point source gases that contain CO2 concentrations between 3% and 25% by volume and produces CO2 with purities greater than 99%, which can then be sold, re-used, or sequestered. The CDRMax™ process uses the company’s proprietary solvent, process equipment design, and advanced heat integration to significantly reduce both capital and operating costs.